How To Properly Maintain Your Commercial Doors
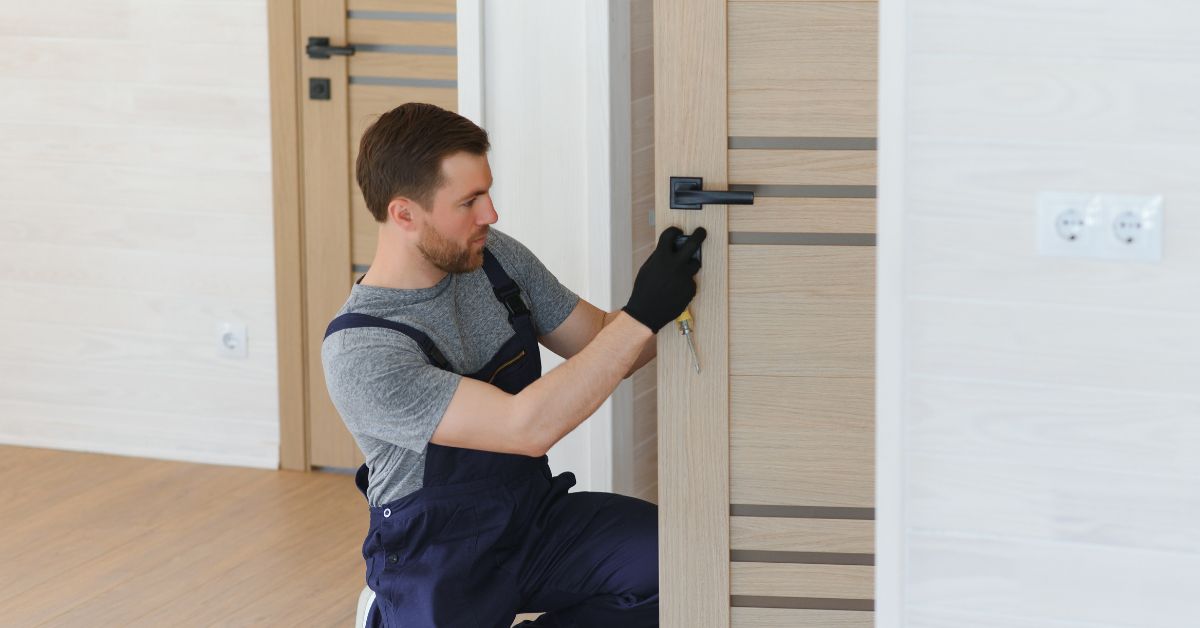
Conduct Regular Inspections
Performing regular inspections on your commercial doors helps you catch issues before they escalate. Inspections don’t need to take up a lot of time, but they require attention to specific areas to maintain function and safety. Here’s what to do.
Look for Visible Damage
Begin with a basic visual evaluation to check for cracks, dents, or misaligned panels. A misaligned door, for instance, can strain its components or interfere with opening and closing. Examine the surface area on both sides to identify physical damage that may worsen if you don’t fix it. Even small dents along metal frames can lead to rust or further disrepair over time.
Check Hinges, Tracks, and Seals
Inspecting commercial door hardware like hinges, tracks, and seals is especially important because wear in these areas affects how smoothly the door operates. Look closely at hinges for signs of rust or loosening, as neglecting these can lead to operational difficulties. Tracks should remain clear and undamaged since bends or debris can block movement. Seals are another priority—tears or cracks may compromise insulation and increase energy costs. For example, a worn seal allows drafts to seep through, making your building less energy efficient.
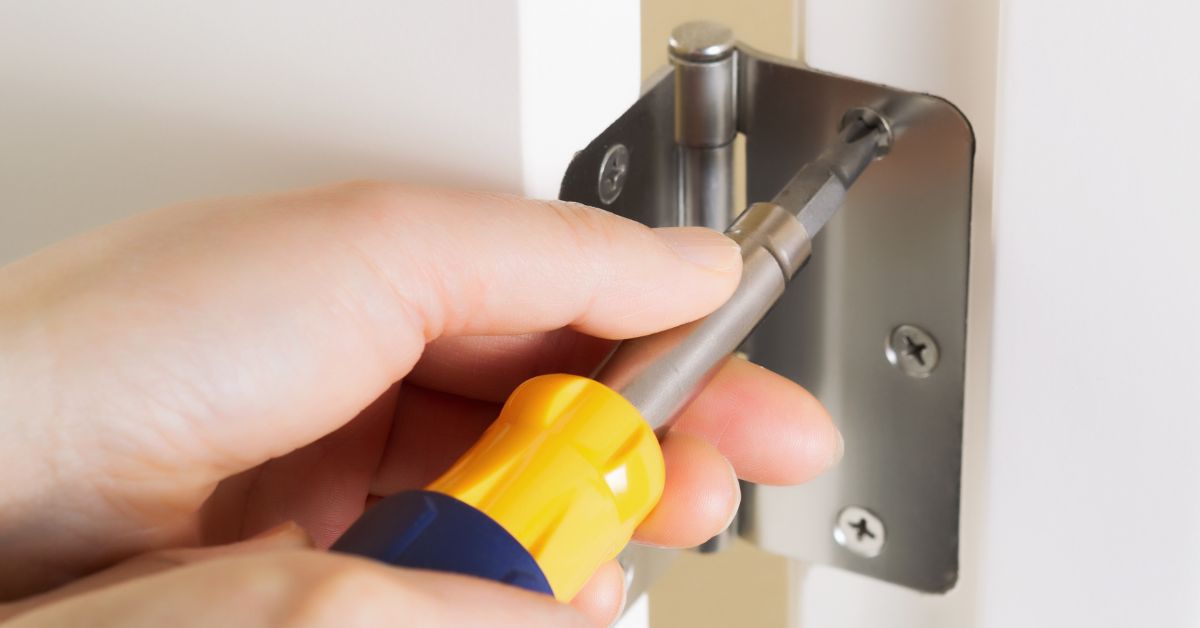
Test Door Movement
Manually open and close the door to observe its movement. Pay attention to any stiffness, resistance, or unusual noises, such as grinding or squeaking, which could indicate internal issues. For instance, stiffness typically comes from misaligned tracks or debris buildup. Note how the door locks, as a poorly functioning lock can pose a security risk. Testing performance during inspections allows you to identify trouble areas quickly.
Examine the Frame
Walk around the door, and check the frame, examining spots that frequently endure wear and tear. Look for any signs of warping in wooden doors or rust developing along the frame of metal ones. A warped frame can leave gaps, while rust can corrode connectors or weaken hardware. Don’t overlook corners, as they collect grime and moisture, which can contribute to structural problems.
Clean Your Doors Routinely
Regular cleaning goes beyond aesthetics. It affects long-term door functionality. First, determine the best cleaning method for your door. If it’s a metal door, use a soft cloth with mild soap to remove surface dirt, then rinse with water to reduce streaks.
For wooden doors, stick to a clean, damp cloth to avoid moisture damage. Glass sections benefit from quality glass cleaner applied with a microfiber cloth, promoting a streak-free shine. Avoid acidic or abrasive cleaners that may damage the door’s finish, especially on painted or powder-coated surfaces.
Moreover, tracks and hinges collect dust and particles from frequent use. You can use a vacuum to remove larger debris stuck in tracks and a damp cloth to clear smaller particles. Pay extra attention to hinge areas that stick or produce noise as debris buildup can compromise movement. For example, grime along door tracks may prevent the door from closing entirely, creating a gap.
Additionally, handles and locks carry visible signs of dirt and smudges from regular contact. Use an appropriate cleaner for the hardware’s material—metal polish works well for stainless steel while soapy water suits other finishes.
Overall, it’s important to stick to a consistent cleaning schedule tailored to your door’s environment. For example, an entrance door in a restaurant will likely need more frequent cleaning than one in a stockroom.
Lubricate Moving Parts
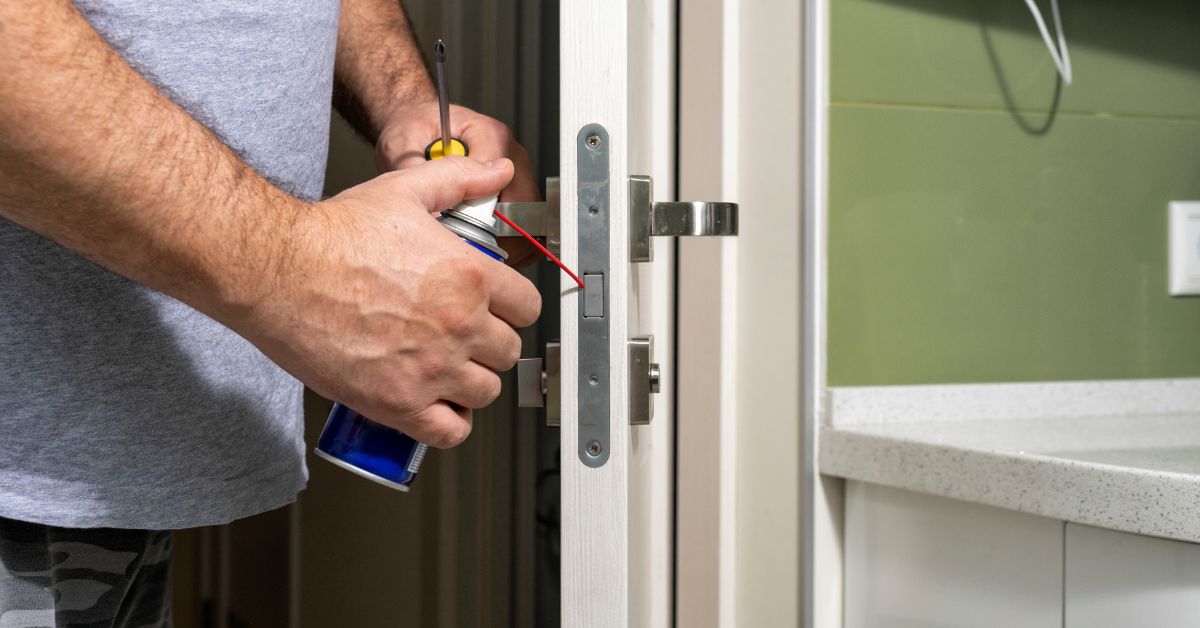
Lubrication supports the smooth operation of your commercial doors. Without it, moving components encounter friction, which accelerates wear and tear. Not every lubricant works on commercial doors, so product choice is important.
Use a silicone-based spray or a product for metal-to-metal contact. Avoid heavy grease or oils that may collect dirt or gum up the mechanisms. For example, a high-performance lubricant for industrial doors will reduce friction without leaving residue that attracts dust.
Spray lubricant in short, controlled bursts directly onto the targeted component. After applying, use a clean cloth to wipe away excess material.
Identify Signs of Poor Lubrication
Here are key signs that indicate your doors need lubrication:
- squeaking noises
- increased effort during operation
- visible dryness on components
- unusual vibrations
- stiff or jerky movements
Tighten and Check Door Hardware
Over time, screws, bolts, and other fasteners naturally loosen with repeated use. Tightening and checking door hardware helps maintain your commercial doors. Inspect the hardware throughout the frame and moving components.
Loose hinge screws can cause wobbling, while handle bolts and locks affect secure closure. If you notice movement or gaps between the hardware and surface, tighten those elements using a screwdriver or wrench.
Replace Worn or Broken Hardware
When hardware has visible wear or breakage, you must replace it. Rusted screws, stripped bolts, or damaged hinges create long-term problems if you ignore them. Install new hardware that matches the original specifications for guaranteed compatibility. For instance, swapping out a rusted handle with a similar but sturdy model prevents further issues like rust transfer to other components.
Keep Tools Handy for Quick Fixes
Carrying out hardware maintenance is easier when you have basic tools nearby, such as screwdrivers, wrenches, or Allen keys. This allows you to correct hardware issues as soon as you identify them. Building these quick fixes into your proactive maintenance plan promotes safe and hassle-free door function. Additionally, make hardware-tightening sessions part of your regular door maintenance schedule.
Perform Safety Checks Regularly
If your doors include automatic sensors, test them for proper function. Place an object, like a box, in the sensor’s path to confirm the door stops and opens. A malfunctioning sensor can lead to accidents, such as the door closing on a person or object. Dust and dirt typically cause sensors to fail, so clean them during these checks.
Furthermore, test each emergency door to confirm it unlatches and opens correctly. A sticking or jamming emergency door poses serious hazards during evacuations. Replace damaged panic bars, inspect seals, and test the doors frequently to confirm they meet local safety standards.
For manually locking doors, confirm that locks turn smoothly and securely each time. A faulty lock might stick or fail to engage, putting security and usability at risk. Apply lubricant to locks that grind or resist turning, and replace worn-out keys.
When you integrate these steps into your routine, your doors remain dependable for years. If you spot a problem beyond your expertise, seek assistance from a commercial door technician.
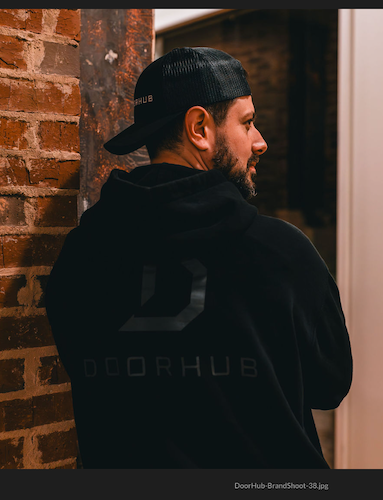
Author
Greg Richard
Chief Technical Officer and Founding Member of DoorHub.com